krdiesel. Proper evacuation must maintain a constant flow of fresh air in one bank, and foul air out the other as this basic training video describes. This is a good video on the basics:
https://www.youtube.com/watch?v=EPIfI9aZHt4The clean side fresh air comes from the one side turbo inlet pipe, but really should come from just after the air filter so it does not overcome the "flushing" or "purging" flow direction of the PCV system. So on the Flex and the other longitudinal oriented engines the cleanside should be tapped into the air box, or the main intake tube just after the air filter so there is little suction, and still filtered fresh air. Then the opposite bank (pass side in truck, rear side in cars) is where these oil/fuel/water/sulfuric acid laden vapors are evacuated. If you allow the turbo inlet to switch the flow direction, this allows these gasses to accumulate and collect in the crankcase causing contamination to the engine oil. So the OEM system works fine at idle and low throttle when zero boost is present, maintaining a constant evacuation of these compounds not allowing them the chance to accumulate in the crankcase. But as soon as the engine begins to make boost, which is quite rapid due to the design of the turbo system and the small size of them, the checkvalve in the pass side valve cover (rear on transverse) closes and then there is NO evacuation taking place. Then blow by produces crankcase pressure that eventually builds to the point that it pushes "out the in" and it is during this time that these compounds accumulate and condense. Then as the pressure is pushing out the inlet, some of this concentrated mix is also drawn with it and sucked into the turbo on that side, and pushed into the CAC where some of it condenses and accumulates there. Since this is backwards of the intended flow path/direction, and there is no opening of an alternative fresh air source from the other bank, most of the mix accumulates in a concentration that causes what you see drained from the cans on the trucks. So, this is similar to a smoke filled room. Open one window, and only a small amount of smoke will escape. Open one on the opposite end of the room and have a fan attached, and the room clears in no time. The easiest way to correct this flaw and retain emissions compliancy, is to simply add an alternate suction source so that there is a nearly seamless switch of evacuation suction source, and the correct direction of flow, and the constant evacuation of the damaging compounds, remains constant so these are removed at a pretty steady rate, and a small amount steadily than a gulp of concentrate.
Quote from: dalum on April 14, 2014, 03:25:33 PM
Per the emissions standards this all has to be self contained so any gasses coming out will get ingested back into the system. The "best" thing would be the off road replacement for the oil cap that is just an air filter. It lets in fresh air and any oil that would be blown back out during reversal hits the inside of the filter and doesn't go anywhere near the intercooler.
It's my understanding our pcv system fails under boost because there is pressure instead of vacuum at the inlet in the throttle body. The inlet into the "intake" port on the valve cover is also too close to the turbo so lower pressure in this region create a small vacuum on this line as well. This vacuum is normally equaled out by the vacuum at the throttle body port so the positive nature of the exhaust port would keep stuff flowing in the right direction under non-boost.
The 2 lines added in front of each turbo serve as the highest vacuum source for the pcv system (through the can) while in boost. The clean side separator's intake (as well as the clean sides intake from the factory) should be to open atmosphere but since thats illegal its placed as close to the main intake filter as possible so it will have as little vacuum on this line as possible.
Excellent understanding!! But the next post would not work correctly. We always want a flow of fresh in one side, foul out the other, but an excellent idea. This is good thinking and understanding all.
The ideal system is a belt driven vacuum pump like we run on all of our alky drag engines.

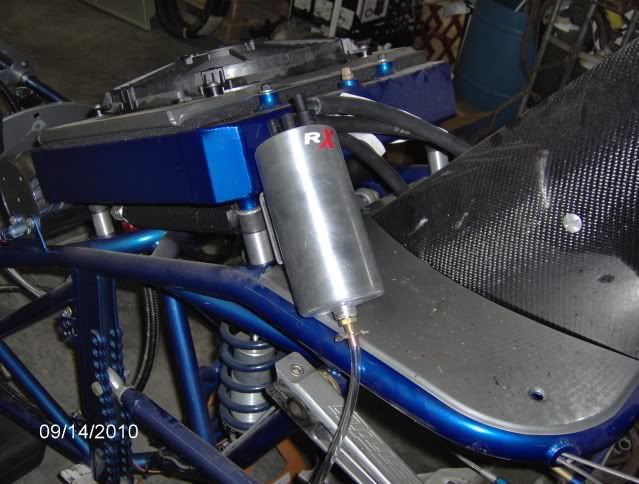
We have the vacuum pump maintain a steady 14-15" of vacuum at all times on the crankcase, this removes ALL water, unburnt fuel, etc. from the crankcase constantly and also reduces the amount of energy required for the pistons to move downward in the bore (why most with the RX system claim more power, etc.) as well as prevent ring "flutter" from pressure (we always want the rings steady and sealing as best they can against the cylinder wall). We have an adjustable vacuum relief valve on the opposite valve cover as we pull from so we maintain the flow direction. The picture above shows the vac relief valve plumbed into the system near the pump. It will maintain vac level, but will not allow cross flow so we changed it's location before installation of the engine in that dragster.